Produce Renovation Packages
5 steps of production, 6 ingredients of the INDU-ZERO factory and 7 steps to create a landscape
The INDU-ZERO will produce 15.000 renovation packages per year. In the following five steps, the digital model is converted into a fully completed renovation package, ready to be transported to the selected houses.

Production
1.
Delivery of materials to the factory
To produce the packages for renovating 15.000 houses per year, an average of 100 trucks a day will be required to bring the inbound materials for the production machines to produce the renovation packages.
2.
Storage of the materials
Shown here is a plan view of the warehouse floor, which will be located on the first floor of the factory. The warehouse floor is divided into three warehouse areas which are connected between them by the goods receipt areas shown in figure 2.
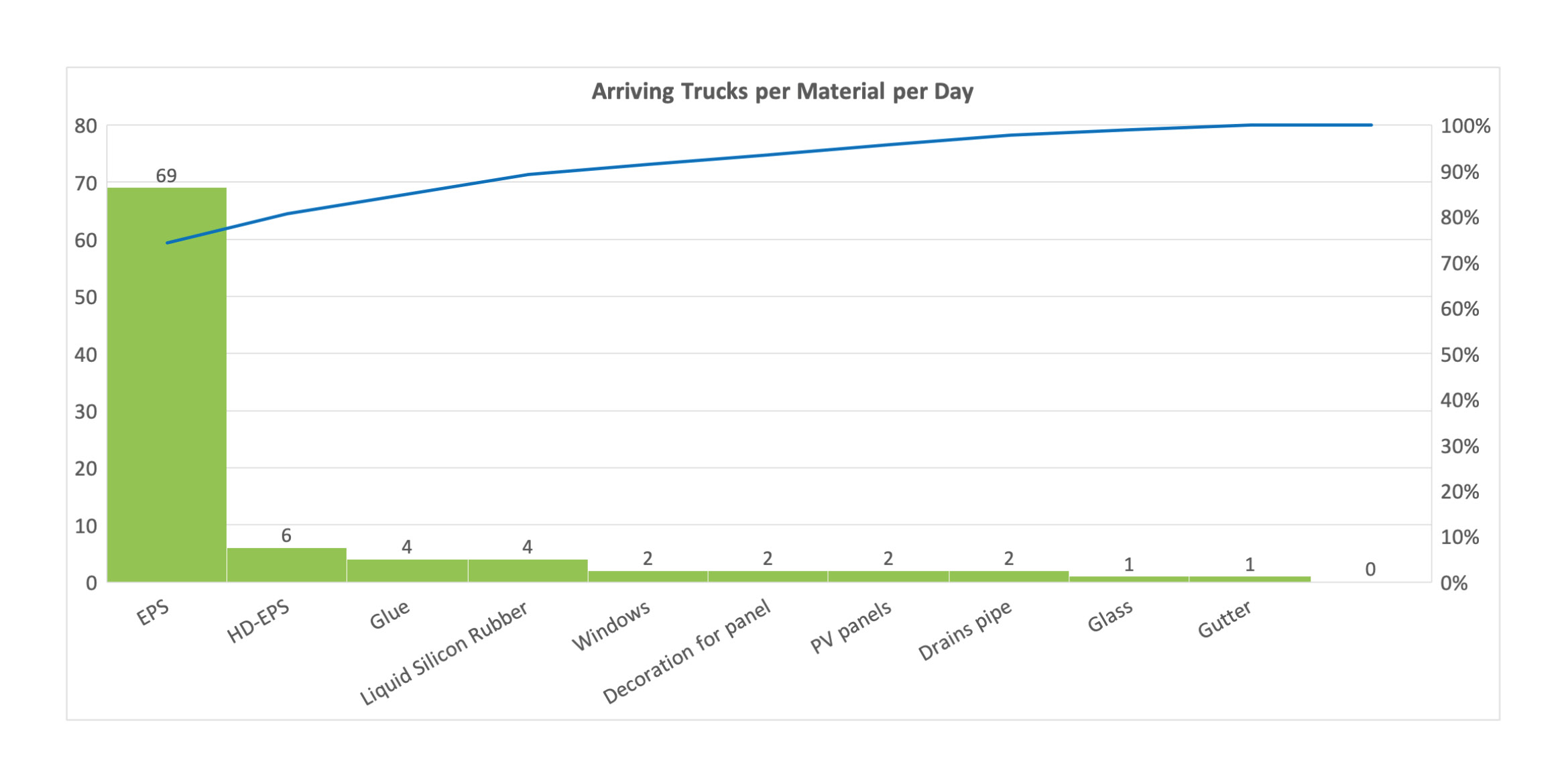
The materials above have the highest percentage of panels and may require daily delivery. The sophisticated and intensive process infrastructure requires precise planning and the latest methods to ensure the handling process is carried out as efficiently as possible. The factory suppliers will mark the inbound materials with barcodes or RFID chips for tracking. All the tracking data will be connected to the factory enterprise resource planning (ERP) system, which works with an automatic order process to ensure all the materials arrive well in advance.
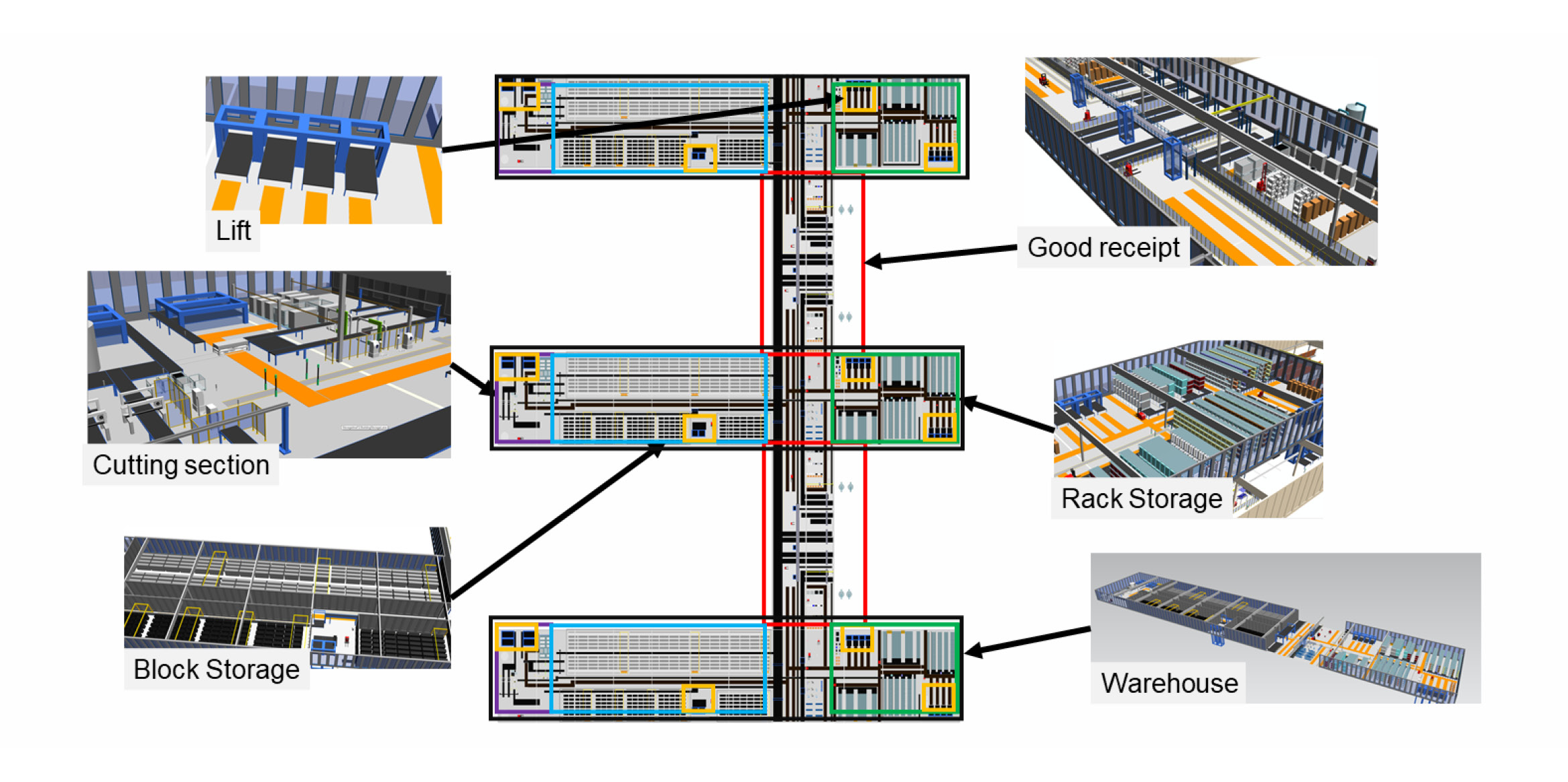
Figure 2 - Indu-Zero in-factory logistic and storage system
The goods receipt areas are where trucks deliver the goods to the factory. The unloading will take place with the help of automatic guided vehicles (AGV) and conveyors. The AGVs (shown in red) locate themselves before the trucks arrive to be ready to unload the freight. The delivery will be unpacked in the goods receipt location and directed to one of the three warehouses before being stored individually to enable just-in-sequence availability for the production process. The EPS panels, HD-EPS boards and HD-EPS profiles will be taken to the EPS storage location, shown on the left-hand side of the plan, and all the other goods such as windows, doors, solar panels, screws, etc. will be taken to their designated storage racks shown on the right-hand side. The warehouse will use a fully automatic loading, storing, and unloading system. When the production floor requests a number of EPS panels, the required number will be transported to the cutting section (shown on the left on the plan) and cut according to the requirement. Lifts and conveyors located on both sides of the warehouse will transport the goods to the production on the ground floor.
3.
Upload data to control the production robots
Selected information from the 3D-model of the preparation phase will be utilised to program the production robots. Various forms of output data can be exported from the model to support the establishment of the instruction sets required to control robotic and autonomous manufacturing equipment. For example, the CNC milling machine is loaded with the instruction set to cut the EPS panel to precise dimensions generated according to the scanning data generated 3D model of a particular renovated house.
4.
Production of roofs and walls
Below shows a plan view of the production floor, located on the ground floor, and houses three independent production lines.
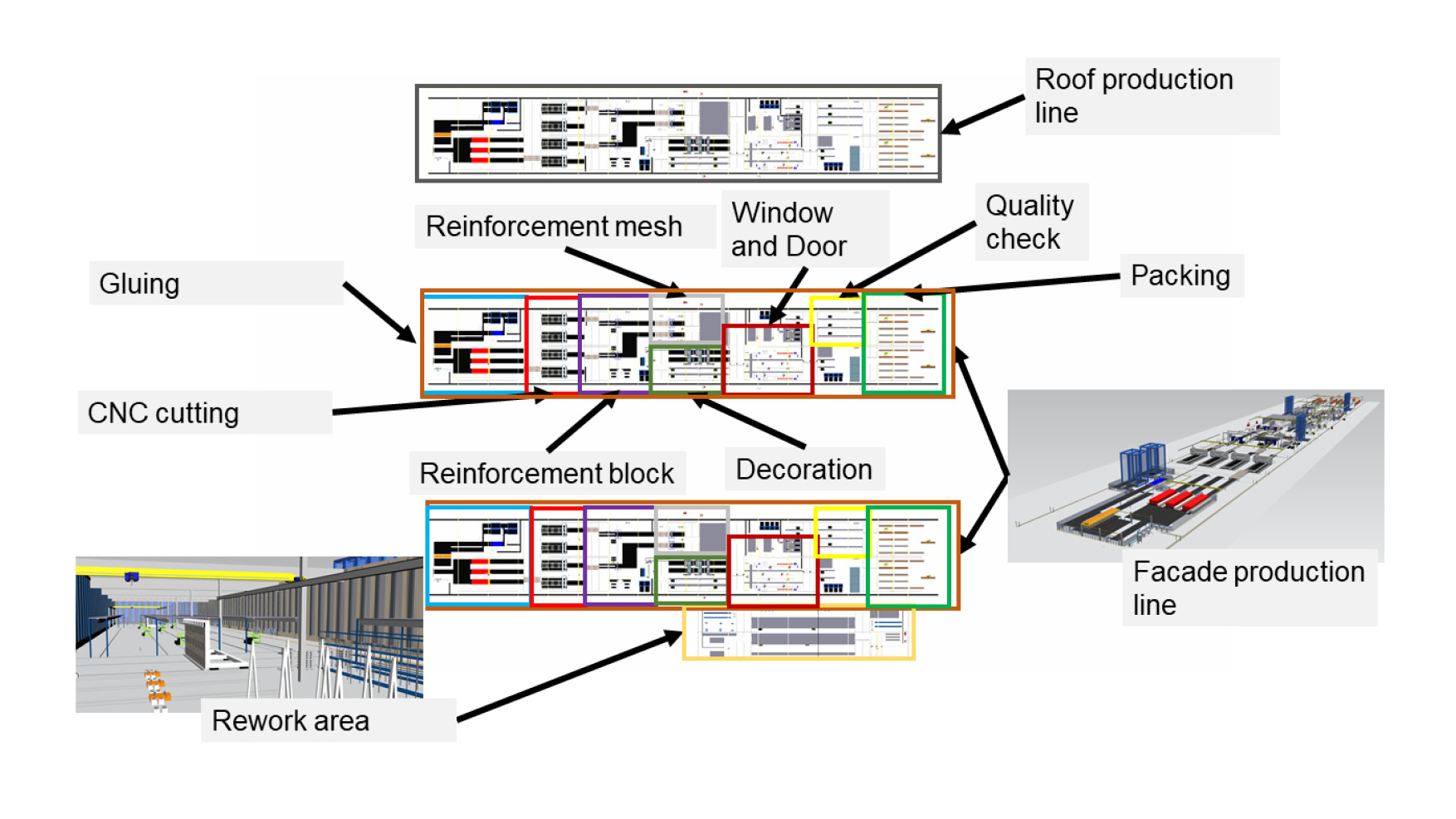
Figure 3 - Indu-Zero manufacturing process blueprint
The ground floor production area will be connected to the first-floor warehouse area via elevators. The different type of elevators can handle the EPS panels, the HD-EPS boards as well as pallets of material such as doors, windows plaster and fiberglass matt. The production floor houses three production lines which are 425 meters long and 66 meters wide. The facade panels will be produced on the first two production lines shown on the top and middle product lines on the plan view in Figure 3. The roof panels are produced on the third production line, shown on the top production line on the plan view. All the materials are delivered just-in-time from the warehouse on the floor above. The production floor also includes a rework area which allows staff to correct any quality issues on the finished product. This area will also be used for research and continuous improvement development.
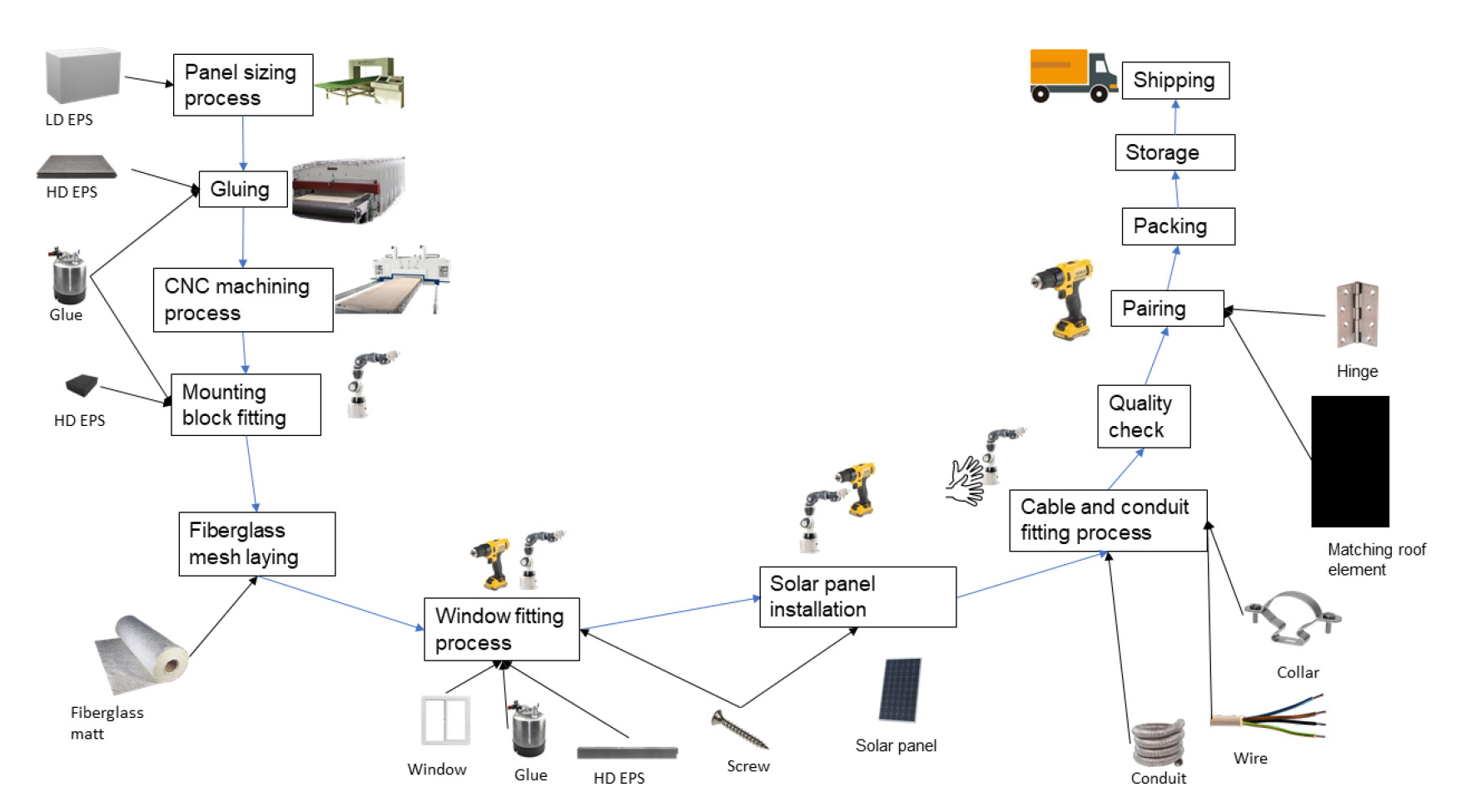
Figure 4 - Manufacturing processes and machineries used
Production of the façade elements requires a number of manufacturing processes shown in Figure 4 and it follows the following steps:
- A wire cutter slices the low-density EPS panels to the right length;
- High-density and low-density EPS panels are glued together and pressed until bonded firmly;
- The CNC milling machine accurately shapes the panels outer dimensions and cuts out the apertures for windows and doors;
- HD-EPS fixation blocks are then attached to the sandwich panel;
- The panel is then reinforced with a fiberglass mesh;
- The external finishing is attached to the sandwich panels, for example tiles, plaster or wood strips;
- Windows and doors are mounted to the panels;
- Electrical cabling is integrated in the panels;
- The quality of the panel is controlled using latest vision based technologies;
- Panels are sorted and packed on racks by bundles;
- The racks with the panel are then stored before the shipment.
The sandwich panel’s modular design for manufacture and assembly is optimised for automation and customisation. All mounting features and cables for attaching solar panels and associated renewable energy system parts are standardised and will be positioned to match the design formed in the 3D model for each home.
5.
Transportation to site
After the INDU-ZERO panels have been produced, this is communicated via the ERP system to the outbound warehouse, the logistics department (trucks) and the construction site. First, the panels are packed separately for each location they are designed for (e.g. house project A) and placed on the load carriers. The load carrier conveys information to the system via the RFID chips or barcodes that the package is ready for internal transport to the outdoor warehouse. The panels are then transported to the storage by AGVs. When the construction site is ready, the truck driver will be informed that the panels can be collected and transported to the construction site.